by Stacy Byrd, CDT, and Kevin P. Kling
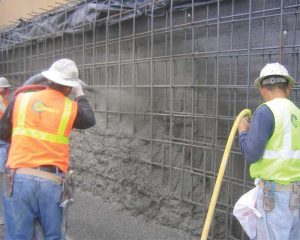
Below-grade construction with shotcrete is gaining popularity across the country. The trend of using shotcrete instead of conventional cast-in-place (CIP) concrete can be attributed to the lower construction cost and time saved by not having to place and remove formwork. However, the use of shotcrete has resulted in a higher incidence of water ingress in below-grade foundations. This appears to be greatest on projects where conventional CIP concrete is value engineered out to shotcrete after the bids are awarded. One may argue this, in part, could be the result of not reviewing or updating the waterproofing system details—initially designed for CIP—for the application conditions associated with shotcrete.
Defining shotcrete
Shotcrete is concrete conveyed through a hose and pneumatically projected at a high velocity on a surface to achieve consolidation. According to the American Concrete Institute (ACI), structural shotcrete has a specified compressive strength of 28 MPa (4000 psi) or greater. It is further defined by the size of the aggregate used, with maximum aggregate grading typically being 13 mm (1/2 in.). Shotcrete can be applied by two processes: dry-mix and wet-mix. With dry-mix shotcrete, dry concrete materials are blended and dampened, placed into delivery equipment, and then conveyed through a hose with compressed air where water is added at the nozzle as the mix is applied. For wet-mix shotcrete, the concrete materials are mixed with water prior to the delivery equipment, and then conveyed through a hose by positive displacement to the nozzle where compressed air is introduced as the mix is applied.
An advantage with the wet-mix process is the ability to better control proportions of the cement, aggregate, and water to maintain mix consistency. Since shotcrete is placed with a high cement to water (c/w) ratio (low slump), it does not require conventional forming. Most structural shotcrete on commercial construction projects is installed using the wet-mix process.
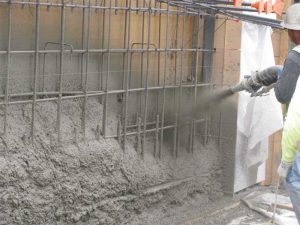
Shotcrete is typically applied from the bottom up to compact and consolidate the working lift. The top of each lift is shaped at a typical one-to-one downward slope. The velocity of the wet-mix shotcrete on ejection from the nozzle is usually around 20 to 30 m/s (65 to 100 ft/s). Structural shotcrete is typically applied at a rate of 4 to 11 m3 (6 to 15 cy) per hour and 203 to 610 mm (8 to 24 in.) wall thickness.
Shotcrete lift height should be limited to approximately 1.2 m (4 ft) to prevent sloughing and sagging. Successive lifts are placed when the previous one has sufficiently set and developed strength to support the next one’s weight. This process then is repeated until the entire foundation wall is placed.
Curing methods of shotcrete vary from no curing to keeping the surface as moist as possible with water and curing blankets for at least seven days to minimize the shrinkage cracking that can form due to the high c/w ratio.
Shotcrete versus CIP
Although the structural properties of shotcrete can be designed to be equivalent to conventional CIP formed concrete, there are potential challenges with the former, especially waterproofing performance. These water ingress challenges can occur with either positive-side membrane systems or with admixtures added to the shotcrete.
A big advantage with conventional CIP formed concrete is that when placed, the fluid material develops sufficient lateral confining pressure to position the waterproofing membrane against the property-line shoring wall. Additionally, the plastic concrete is vibrated to solidify, thus removing poorly consolidated pockets and assisting the material to flow around and encapsulate reinforcing steel and other structural and mechanical elements. Another advantage is conventional formed concreting does not require the same level of reinforcement stabilization as with shotcrete, so there is no need to pierce the waterproofing membrane with fasteners, thereby eliminating hundreds, if not thousands, of punctures.
With shotcrete, there is less lateral confining pressure on the waterproofing membrane than CIP concrete due to the low slump in which it is applied. Further, without vibrating the shotcrete, voids behind the reinforcement steel and rebound pockets remain unconsolidated. These issues are exacerbated with congested reinforcement steel.
Proper consolidation of shotcrete directly against a smooth waterproofing membrane on a blind-side application can be difficult because pillowing and bridging of the membrane can increase rebound of the concrete, resulting in poor consolidation and rebound pockets along the interface with the waterproofing.
Insufficient time between shotcrete lifts may result in plastic material sagging or bowing away from the waterproofing membrane, creating a potential for voids between the waterproofing and the wall. Shotcrete walls with sagging are susceptible to water ingress because the waterproofing may unattach.